- Norway
- Go to acciona.com
- On Follobanen, ACCIONA has implemented an innovative planning management systemthat both cuts CO2 emissions and can increase efficiency by as much as 25 per cent. ACCIONA now wants to apply the methodology in all major projects companies are involved in.
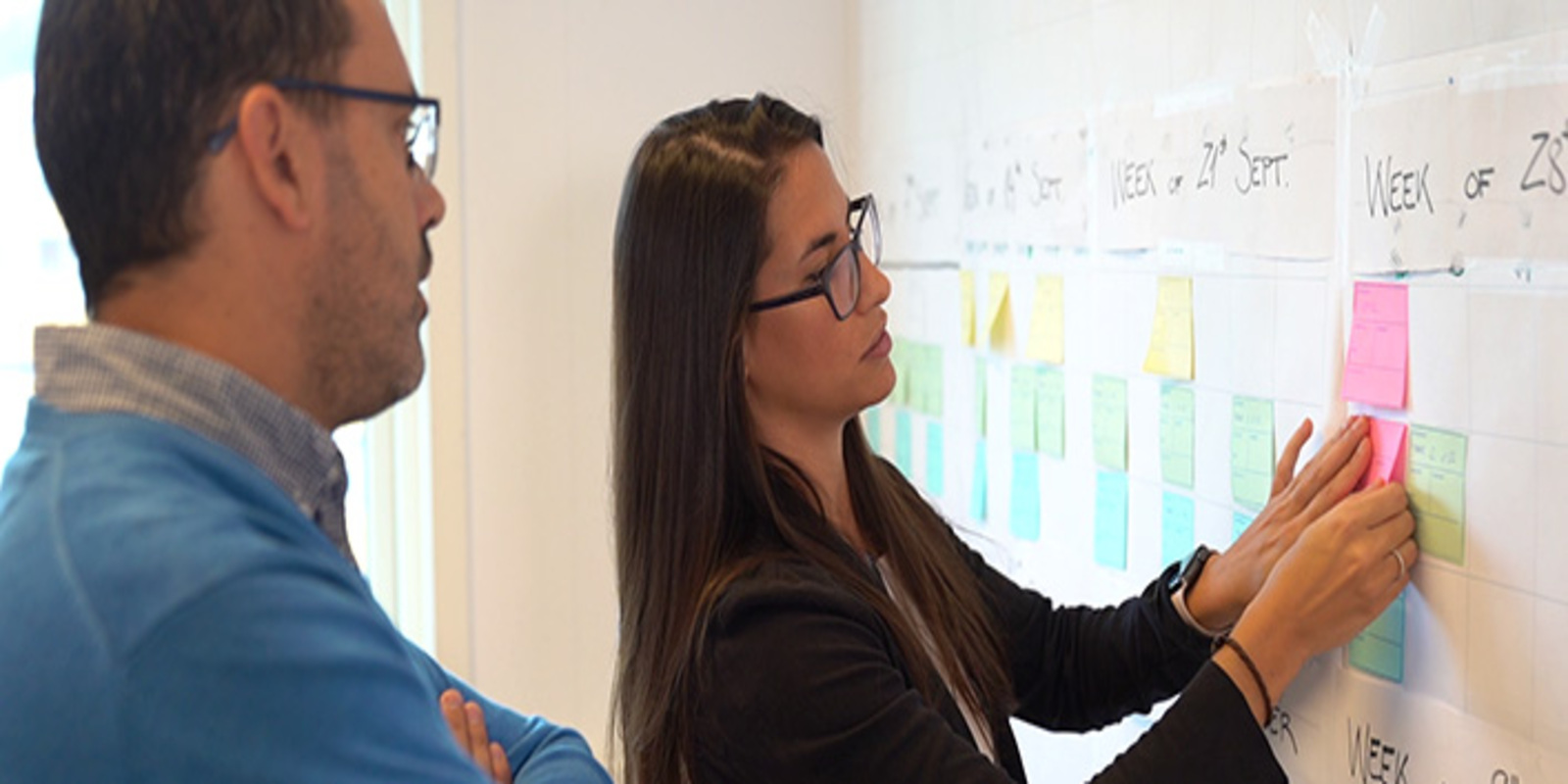
Follobanen was the first project where ACCIONA used this methodology in Norway. " The experience shows that we can increase the efficiency of some activities by as much as 25 per cent when it is fully implemented,though due to the impacts of Covid in the last two years it is difficult to assess" says Juan Medina, project director.
Through systematic use of the planning methodology, the company facilitates more efficient ways of managing and planning large building and construction processes. Since the system was introduced on the Follobanen three years ago, it was also introduced on the E6 Ranheim-Værnes project, where ACCIONA is the overall contractor.
Improved collaboration, transparency and coordination are an essential part of the background for the new system, where everyone have a say in the process of producing the schedules. At the same time, it is about something as fundamental as improving communication between people, Project Director continues.
"The fact that ACCIONA is present on five continents allows us to collaborate and learn across countries and cultures. At the same time, it increases the need for good coordination and planning" , says Juan Medina.
Cuts CO2 emissions
The system includes a collaboration-based method called the Last Planner System (LPS®), making it possible to create realistic plans for and by the production team. The fact that projects can be carried out more efficiently also reduces CO2 emissions.
“Efficient and systematic planning helps us avoid re-work and unnecessary transport. It's a win-win. We thus save on expensive and inefficient transport, at the same time as we cut fuel consumption and CO2 emissions”, says Juan Medina.
“One of the main challenges on the Follobanen was coordinating the electromechanical tasks performed by the main contractor and relevant subcontractors. Every day, we coordinated more than 30 teams from more than 10 different Subcontractors. Coordinating these works was highly complex given the access restrictions that prevented us from overlapping various activities on a single section of the tunnel, further complicated by having a single vehicular access point to each tunnel”, Juan Medina says that the experiences from Follobanen are very promising.
“Thanks to LPS®, we were able to carry out the work in a structured and coordinated way. The method’s success meant that we would also use it in other projects here in Norway”.
Courses employees internally
As part of the planning system, ACCIONA will offer its employees training in the company’s innovative methods. The methods are based on the principles of the Lean methodology. It is all about taking the proper steps for a more sustainable implementation of building and construction projects, both financially and for the climate and environment.
“We want the employees to have the opportunity to develop their skills and create a culture for attitude change. At the same time, we hope to generate the knowledge needed to build and expand the Lean methodology in ACCIONA so that we can take new steps to cut emissions and make more efficiently, better and cheaper”, says the Project Director.
By participating in the course, ACCIONA's employees will have the opportunity to develop key skills in project planning. The starting shot for the course is in September and consists of 40 hours of theoretical introduction. The employees will also gain practical experience through participation in projects that span four months.
“We are convinced that more systematic and better project planning can provide significant benefits for the company, our employees and society”, Juan Medina concludes.